To separate the disc( rotor ) from the hub, the rivets on the front discs have had the heads on the hub side machined off on a lathe, using a hammer & centre punch, knock the remaining part of the rivets through the hole.
|
The discs have been drilled and the holes chamfered to help disperse water as the standard discs are useless for about 5 seconds in the wet. Once separated the disc can be put on a surface grinder and easily ground flat and remove any scoring. |
The holes have been drilled on a radius and the pattern are positioned from a rivet hole so both disc hole patterns will match up when on the wheel, or should do if I have done my calculations right.
|
The disc centres have been stripped just need to sand blast, etch primer and powder coat in silver.
|
Machined 18 bolts to replace the rivets. These are stainless steel, M6 thread and shaft is 6.2mm which is the size drill I used to clean out the rivet holes.
|
Machined the brake caliper dust seal ring from stainless.
|
The dust seal ring is a push fit as is the original one and can be removed again with 2 screwdrivers gently prizing out from two sides.
|
The old pistons were a little pitted so had a go at making my own as not keen on the solid ones you can buy. Machined the brake caliper piston from stainless steel with a brass cap. Piston hollowed out and weight within 10 grams of original piston, the solid ones are about 220 grams heavier.
|
Press fitted the brass cap in to the piston
|
New seal is fitted, seal and piston smeared with brake fluid and piston should glide in with minimal effort.
|
Stainless steel torque arm, made from 16mm tube and 5mm plate, stepped bung at each end, welded with stainless filler rods.
|
Polished and ready to fit.
|
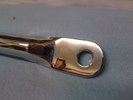 |
|
  |
|
|
|